Tesla подала пример: Toyota тоже будет отливать крупные детали электромобилей под давлением
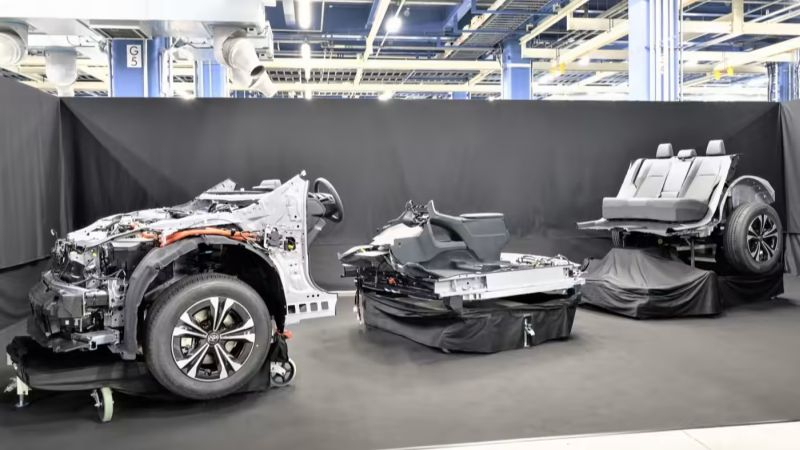
На ранних этапах становления бизнеса Tesla японская корпорация Toyota была акционером компании и помогала ей с проектированием силовой установки электромобилей, но теперь пришла пора крупнейшему автопроизводителю поучиться у компании Илона Маска (Elon Musk) передовым технологиям выпуска кузовных деталей. Последние Toyota также собирается отливать под давлением, как и Tesla.
По крайней мере, представителям Nikkei Asian Review уже удалось увидеть в действии прототип литейного оборудования, которое позволит Toyota Motor сократить затраты времени на изготовление трети основания кузова электромобиля с нескольких часов до примерно трёх минут. Попутно количество обрабатываемых деталей в новом варианте техпроцесса сократится с 86 до 1 штуки, а более 30 технологических операций попросту удастся исключить.
В традиционном варианте крупные сборочные единицы в структуре кузова автомобиля получаются из штампованных фрагментов, которые свариваются или склеиваются между собой, а также крепятся на резьбовых соединениях. Формируя за один проход монолитный фрагмент основания кузова методом литья под давлением, производитель исключает множество промежуточных операций, каждая из которых требует своей технологической оснастки и затрат времени. Точность геометрических параметров монолитной детали повышается, снижается риск брака при производстве, а сам процесс изготовления кузова транспортного средства значительно ускоряется. В частности, прототип литейного оборудования с использованием мощного пресса, который Toyota продемонстрировала журналистам, заднюю часть основания кузова изготовил за три минуты против нескольких часов.
Естественно, такой метод обладает и своими недостатками. Во-первых, крупные прессы занимают много места и требуют соответствующих определённым требованиям производственных помещений. Во-вторых, они дороги в производстве и приобретении, а весьма дорогую оснастку для литья одной детали в итоге можно использовать при производстве лишь ограниченного ассортимента моделей электромобилей, если вообще в этом случае уместно говорить об унификации элементов кузова. Наконец, монолитная деталь менее ремонтопригодна, а это свойство наверняка озадачит специалистов по кузовному ремонту и страховые компании.
Впрочем, судя по энтузиазму, в которым Tesla и Toyota движутся в сторону внедрения таких технологий, вопрос с их применением уже не подлежит обсуждению. Если в случае с компанией Илона Маска можно говорить об ограниченном ассортименте моделей, которые редко модернизируются и выпускаются в огромных количествах, то целесообразность выпуска монолитных кузовных деталей таким методом не оспаривается. Toyota тоже выпускает машины в огромных количествах, ведь пока это крупнейший автопроизводитель в мире, но у неё гораздо шире ассортимент моделей, а подготовка литейной оснастки под каждую модель является дорогим удовольствием. Решится ли Toyota на унификацию конструкций своих машин, либо придумает, как экономить на выпуске оснастки, пока сказать сложно, но в её бизнес-модель такой метод производства кузовных элементов встраивается гораздо сложнее.
Toyota планирует применять технологию литья под давлением больших кузовных элементов с 2026 года при производстве электромобилей на новой платформе. К 2030 году до половины выпускаемых компанией ежегодно 3,5 млн электромобилей должны будут перейти на такую технологию. По крайней мере, переднюю и заднюю часть основания кузова этих машин Toyota попытается унифицировать, а средний сегмент будет уникальным для ряда моделей, позволяя варьировать как длину колёсной базы, так и ёмкость тяговой батареи, которая традиционно будет размещаться под полом салона. Кстати, первый прототип установки для литья кузовных деталей под давлением Toyota изготовила ещё год назад, так что нельзя утверждать, что в этой сфере она сильно отстаёт от Tesla.
Ещё одним ноу-хау при сборке электромобилей Toyota сделает самодвижущиеся сборочные единицы (на фото выше), которые позволят отказаться от использования традиционного конвейера. Шасси будущих электромобилей с батареями, силовой установкой и колёсами будут сами передвигаться по заданной траектории по полу цеха, а расстановленные на маршруте манипуляторы будут закреплять на этой платформе прочие конструктивные единицы и элементы салона. Постепенно будет собран полноценный электромобиль, который сможет отправиться на участок контроля качества.
Такой подход к организации сборки машин позволит Toyota гибко реагировать на потребности рынка, масштабируя объёмы выпуска сообразно спросу и сокращая неизбежные при простоях постоянные издержки. Время, необходимое на сборку одного электромобиля, сократится в два раза до пяти часов. Новые модели при таком подходе тоже удастся выводить на рынок быстрее.
В прошлом году Toyota реализовала около 24 000 электромобилей, но уже в 2026 году планирует продать не менее полутора миллионов, а к 2030 году их количество увеличится до 3,5 млн штук в год. Новые производственные методы позволят автогиганту успешнее конкурировать с более молодыми игроками рынка.
Источник